Introduction
- PowerFlex 4-class drives and PanelView™ Component graphic terminals for your small machine applications. In this section you will perform the following: Connect to the PowerFlex 525 drive through the embedded EtherNet/IP via Connected Components Workbench software.
- PowerFlex 40 Adjustable Frequency AC Drive This Quick Start guide summarizes the basic steps needed to install, start-up and program the PowerFlex 40 Adjustable Frequency AC Drive. The information provided Does Not replace the User Manual and is intended for qualified drive service personnel only.
- We learn by this video,how to set the parameters in drive, how to enter in program mode.
- RS485 (DSI) Protocol Parameter Configuration The following PowerFlex 4M parameters are used to configure the drive to operate on a network. Parameter Details Reference P106 Start Source Set to 5 “RS485 (DSI) Port” if Start is controlled from Page 3-9 the.
Programming of Basic Parameters: Operating Voltage Frequency Motor Full load current Min. Frequency Start source Speed reference Relay Output Etch.
Variable Frequency Drives are used within the automation industry to drive induction motors with added precision over a simple contactor. Over the last decade, these devices have become increasingly cheaper. Based on this phenomenon, it’s now recommended to utilize a VFD over a contactor in every application. VFDs are flexible, provide additional control and data in every application.
The PowerFlex 525 series of Variable Frequency Drives from Allen Bradley are an excellent choice & have been an industry standard for several years. Their reliability as well as ease of use, especially within the Rockwell Automation ecosystem, has allowed them to become popular all over the world.
Comissioning a PowerFlex 525 VFD is straightforward. These drives can be easily wired to start and stop from push buttons through direct inputs. However, a much more practical approach is to add the drive to a private network which includes a Programmable Logic Controller. By doing so, the programmer is able to create advanced motion routines in addition to the simple start and stop features. In this tutorial, we’ll take a look at how to integrate a PowerFlex 525 VFD into RSLogix Studio 5000 over EtherNet IP.
PowerFlex 525 Variable Frequency Drive Basic Wiring and Parameters
PowerFlex 525 VFD DataSheet: Click Here
Within the datasheet, the user will find a lot of information about the setup of the drive. This includes wiring diagrams as well as parameters which we will be setting up shortly.
In terms of wiring, the simplest method of controlling the drive without a PLC is through the use of a start and stop push buttons. The diagram below (taken from the manual) illustrates how this can be accomplished. Note that although this method is simple, it’s not the recommended way to use these drives.
Note that there’s a pre-installed jumper between terminals 01 and 11. This jumper needs to be in place while the drive is controlled over EtherNet/IP. If you’re planning on using pushbuttons, the jumper must be removed.
Within the datasheet, you’ll find parameters which may be configured to suit a specific application. These parameters are split into six sections:
- Basic Display
- Basic Program
- Terminal Blocks
- Communications
- Logic
- Advanced Display
Each section has specific parameters for the drive. As the names suggest, parameters within a section will address the setup of electrical parameters, communication with other devices, logical programming and the display of the drive.
Controlling PowerFlex 525 Drives over EtherNet IP
Establishing EtherNet IP connectivity to a PowerFlex 525 drive requires us to set the IP address and the subnet mask. However, the drive may take an IP address setting from Rockwell’s BOOTP Utility or the parameters. Therefore, we must start with the following:
- Set C128 to 1 “Parameters”.
By setting C128 to 1, as the figure above illustrates, we’re telling the drive to look at the parameters for the IP address over BOOTP.
Digimon data squad full episodes. The next step is to give the drive an IP address. This is achieved through the following steps.
- Set C129 to the integer of the first octet.
- Set C130 to the integer of the second octet.
- Set C131 to the integer of the third octet
- Set C132 to the integer of the fourth octet.
By setting those four parameters, the IP of the drive will be as follows: C129.C130.C131.C132. Example: 192.168.1.7
The next step is to give the drive a subnet mask. This is achieved through the following steps.
- Set C133 to the integer of the first octet.
- Set C134 to the integer of the second octet.
- Set C135 to the integer of the third octet
- Set C136 to the integer of the fourth octet.
By setting those four parameters, the subnet mask of the drive will be as follows: C133.C134.C135.C136. Example: 255.255.255.0
Lastly, we need to re-boot the drive for the address to take:
Did you know I have a Channel with more cool videos like this? Showing customers in audience, DJ, Bouncer in Lap Dance Room, and dancers. Sims 3 pole.
- Set P053 to 4 “Module Reset”
By setting this parameter to 4, the module is reset without affecting the memory of the drive. This is a required step in order for the drive to set the parameters we’ve given it in the previous steps.
Wiring Start Stop Push Buttons into CompactLogix Allen Bradley PLC
Now that the PowerFlex 525 VFD is controlled through EtherNet/IP, we need to add external controls to our PLC. We will be adding a start and stop push buttons to control our drive through some basic ladder logic. The L24ER-QB1B PLC is equipped with Inputs and Outputs directly on the main hardware. Since we’re only using push buttons for this example, we only need to worry about the inputs.
The PLC inputs may be configured as sourcing or sinking. This concept is often missunderstood by engineers and technicians. However, the datasheet of the PLC provides a comprehensive diagram. Furthermore, a simple pushbutton may be wired to be a pseudo PNP or NPN device. The reason we say “pseudo” is that a push button doesn’t contain a transistor and is simply driving the voltage High or Low. A PNP or NPN designation is typically used in case of a sensor which uses a transistor.
The image obove displays both configurations with the sinking one highlighted. Furthermore, the two inputs, 00 and 01, are shown as well. These inputs are used for the start and stop button.
Page 1 STIH) STIHL FS 80, 85 Instruction Manual Manual de instrucciones Warning! For safe operation follow all safety precautions in Instruction Manual - improper use can cause serious injury. Para su seguridad durante el manejo de este producto, siga siempre las precauciones de. Page 1 All manuals and user guides at all-guides.com BAFS8082UH4.book Seite 0 Dienstag, 3. August 2004 7:52 07 STIH) STIHL FS 80, 85 Instruction Manual Notice d’emploi. FS 80, FS 80 R, FS 85, FS 85 R Pictograms All the pictograms attached to the machine are shown and explained in this manual. The operating and handling instructions are supported by illustrations. Symbols in text The individual steps or procedures described in the manual may be marked in different ways:: A bullet marks a step or procedure. Stihl fs 80 service manual.
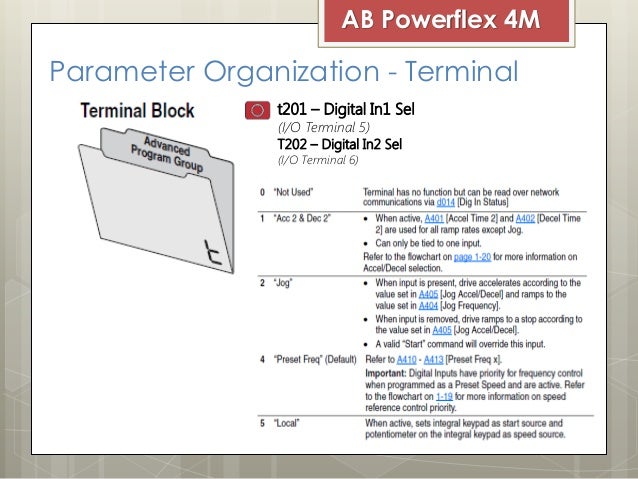
The image above is the actual PLC with the common landed on the 0VD terminal and the two buttons landed on the inputs 00 and 01.
On the button side, the Start button is wired as normally open while the Stop button is normally closed. This is the typical wiring scheme based on a hardware circuit configuration. This can be achieved by selecting an appropriate button type or by selecting the ones that have either option available. Note that through software, you may program the buttons to work in any configuration; our typical preference is to keep all buttons normally open.
Once the PLC is powered up, the inputs are tested. The normally closed input should be “High” while the normally open one should be “Low”. Once either button is pressed, the input should transition to the opposite state.
Adding the PowerFlex 525 VFD to RSLogix Studio 5000
We’ve placed the drive onto the same physical network as the PLC and gave it an IP address which allows it to communicate to the controller. We now need to configure the drive through the software in order to program the control. This is achieved through RSLogix or Studio 5000 depending on the flavor of the PLC used in the control system. However, the steps should be the same with minor differences due to firmware revisions.
Step 1 – Adding the drive to the IO tree
By right-clicking the EtherNet node of the PLC, it’s possible to “Add a New Module”. Once the window is opened, find the device you wish to add by searching in the specified area or by scrolling down through the list. Note that you may need to install the drivers on older PLCs. They can be found through the Rockwell Automation download center and installed on the local machine which has RSLogix or Studio 5000.
Step 2 – Configuring Parameters
Once the drive is added & the hardware is properly connected to the controller, it’s possible to configure the internalt drive parameters through RSLogix Studio 5000. Note that if the IP, subnet mask or the physical network aren’t correct, the user won’t be able to access the parameters at all.
Configuring the parameters is done based on the datasheet. For a simple control scheme it’s enough to set the drive to be controlled over EtherNet/IP and set the correct Voltage levels based on the motor. It’s recommended to verify the physical setup of your specific control system before proceeding with testing a live motor.
Note that the same parameters are displayed in this prompt as the ones we accessed through the drive at the start of the tutorial. You may change them through the drive or through the programming interface. For obvious reasons, it’s much simpler to change them through RSLogix Studio 5000.
Programming Start Stop Ladder Logic in RSLogix Studio 5000
We’ve shown an example of programming a simple start and stop routine in one of earlier videos, but in this case, we’re using buttons which aren’t both normally open and the drive has tags which are generated by the software.
Powerflex 4 Parameter Spreadsheet
Here’s what the tag structure of the PowerFlex 525 Drive looks like when the drive is added into the program:
Each one of these tags can be used as an Input/Output in order to control the drive in a certain way. However, the most utilized and needed tags are Start, Stop, ClearFaults, Forward, Reverse, FreqCommand and the output tags for diagnostics. Note that it may be confusing by the nomenclature, but the tags labeled as O are PLC outputs, drive inputs. The opposite is true of the tags labeled as I. In other words, they’re inputs and outputs depending on what the reference is taken.
The logic you choose to write is entierly up to you, but at the very least, you’d want to start and stop the motor. Beyond that, you can implement speed control and forward/reverse if needed. Lastly, you’d want to implement a way to incoporate the input tags into your routine to detect faulted conditions. You may choose to add advanced routines which would monitor the acceleration and deceleration to fine tune what the drive is doing.
Here’s the logic to get the motor to start and stop based on the two buttons we’ve added earlier in the tutorial:
Conclusion
Selecting a Variable Frequency Drive over a contactor should be a no-brainer in most current applications. In the Allen Bradley selection, the most commonly used VFD is a PowerFlex 525 for small motors. Similar part numbers are available for larger drives. This drive is easily networked onto the plant infrastructure and communicates to the PLC over EtherNet/IP.
By building a small motor starter circuit in this tutorial, we’ve demonstrated the ease at which one can add a PowerFlex 525 VFD to the RSLogix Studio 5000 PLC Program running on an L24ER-QB1B processor. The VFD is programmed to start and stop based on the presses of the two buttons wired into the local inputs of the same PLC.
Powerflex 4 Parameters
Powerflex 4 Vfd Manual
Video Tutorial
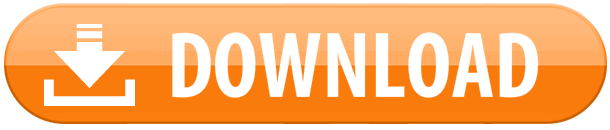